Mirror
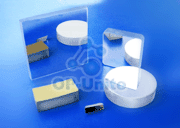
Mirror is
a smooth, highly polished surface, for reflecting light, that may be
plane or curved.
The actual reflecting surface is
usually a thin coating of silver or aluminum on
glass.
OP-Unite designs and manufactures a great choice of various high
and partially reflecting mirrors for the spectral range: UV,
visible, near infrared, and infrared regions. Metallic coatings are
more broadband while dielectric coatings are more efficient.
Selecting the proper mirror for your application requires
making a number of choices. A few of the many considerations
include: Reflectivity, Laser Damage Resistance, Coating Durability,
Thermal Expansion of the substrate, Wavefront Distortion, Scattered
Light, and certainly Cost. The following tables should help in
comparing the available choices from OP-Unite.
Featured
substrate materials:
Pyrex is an excellent mirror substrate due to
its low coefficient of thermal expansion and resistance to thermal
shock. When high stability is critical, Zerodur is the best choice
for its zero thermal expansion. UV Fused Silica has a thermal
expansion coefficient lower than Pyrex, yet is more expensive.
Because of its excellent transmissive properties, it is often
reserved for transmissive mirrors as well as high-energy laser
mirrors.
CZ Silicon is frequently used for laser mirrors
because of its high thermal conductivity and low density.
OP-Unite can provide Metallic Mirrors and Dielectric Mirrors
such as Metal Coated Mirrors, Flate Plates HR Mirrors, Flat Plate
Hormnic Separators and other Laser Line Mirrors. The types we supply
includes: Plate Mirrors, Spherical Mirrors.
Material |
Coefficient of Thermal Expansion |
Cost |
Features |
BK7 |
7.5 x 10-6/¡ãC |
Low |
High homogeneity and low bubble and inclusion
content. |
Pyrex |
3.25 x 10-6/¡ãC |
Low |
Best all around mirror substrate, low expansion
borosilicate glass, resistant to thermal shock |
UV Fused Silica |
0.52 x 10-6/¡ãC |
High |
Low thermal expansion for excellent stability,
high laser damage resistance |
Zerodur |
0¡À0.1 x 10-6/¡ãC |
Moderate |
Nominally zero thermal expansion for ultra-high
stability, unique glass-ceramic material |
Silicon |
1.20~8.00um |
Moderate |
High thermal conductivity and low
density |
Optical
surfaces requirements:
The mirror application drives the
requirements for surface irregularity and surface quality.
Surface Flatness |
Figure |
Cost |
Applications |
¦Ë/2 |
Low |
Used where wavefront distortion is not as
important as cost. |
¦Ë/5 |
Moderate |
Excellent for most general laser and imaging
applications where low wavefront performance must be balanced
with cost. |
¦Ë/10 |
Moderate |
For laser and imaging applications where low
wavefront distortion, especially in systems with multiple
elements. |
¦Ë/20 |
High |
For the most demanding laser systems where
maintaining accurate wavefront is critical to
performance. |
Surface Quality |
Scratch-Dig |
Cost |
Applications |
60-40 |
Low |
Used for low-power laser and imaging
applications with unfocused beams where scatter is not
critical. |
40-20 |
Moderate |
Ideal for laser and imaging applications with
collimated beams where scatter begins to affect system
performance. |
20-10 |
High |
Excellent for laser systems with focused beams
that can tolerate little scattered
light. |
Angle of
Incident (AOI):
Usually the Angle of Incident (AOI) are 45 degrees
or 0 degree as follows:
Following mirrors are what OP-Unite can provide:
Manufacturing Tolerances:
Tolerances |
Commercial quality |
Precision quality |
Manufacturing limits |
Diameter (mm) |
+0/-0.10 |
+0/-0.025 |
+0/-0.010 |
Scratch-Dig |
80-50 |
40-20 |
10-5 |
Power (fringe) |
3 |
1 |
0.2 |
Irregularity (fringe) |
1 |
0.5 |
0.1 |
Parallelism |
- |
3~5 arc min |
Facility controlled |
Bevels |
Upon requirement |
No bevel |
Coatings |
Upon requirement |
Note: Cutting Mirrors, Square Mirrors, Rectangle
Mirrors are upon requirement. Plano Mirror, Spherical Mirror,
Cylindrical Mirror are upon requirement.
The general tolerance
specifications above provide a guideline regarding manufacturing
capabilities for optics ranging in size from 1-300mm. The
manufacturing limits are not absolute; tighter tolerances may be
possible. Part specific tolerances may vary depending on component
size, shape, and/or material.
|